Just how to Identify What is Porosity in Welding and Improve Your Strategy
Wiki Article
Porosity in Welding: Identifying Common Issues and Implementing Finest Practices for Avoidance
Porosity in welding is a pervasive problem that typically goes undetected up until it triggers considerable problems with the honesty of welds. In this conversation, we will check out the crucial aspects contributing to porosity development, examine its harmful results on weld performance, and discuss the finest techniques that can be adopted to lessen porosity occurrence in welding procedures.Typical Root Causes Of Porosity
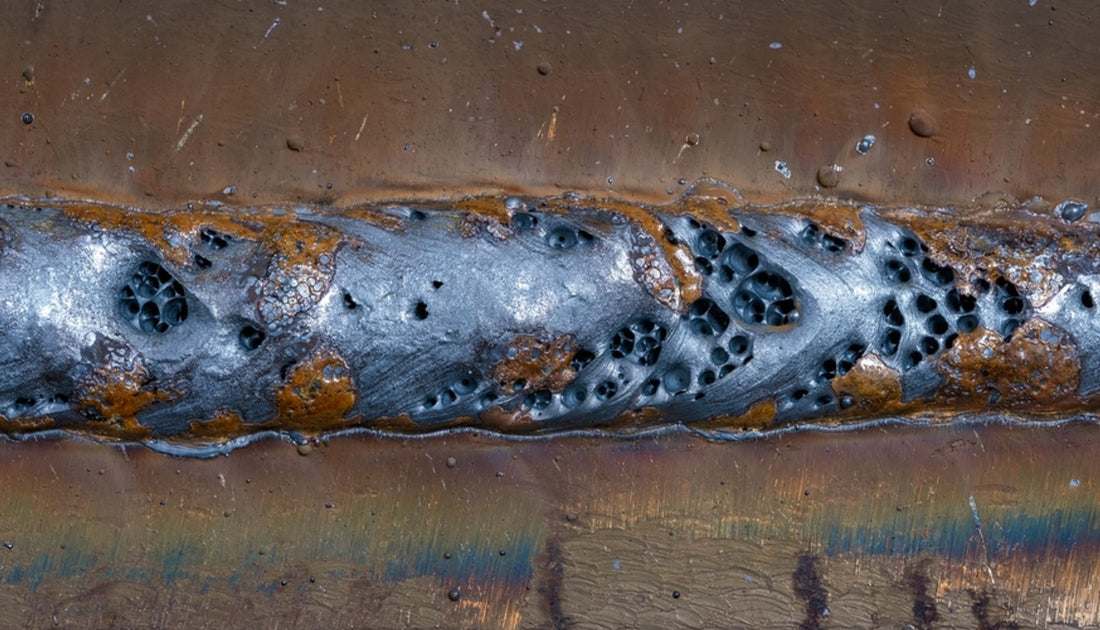
Using filthy or damp filler products can introduce pollutants right into the weld, contributing to porosity problems. To minimize these common reasons of porosity, thorough cleaning of base steels, correct shielding gas choice, and adherence to optimum welding criteria are necessary techniques in accomplishing premium, porosity-free welds.
Effect of Porosity on Weld Quality

The visibility of porosity in welding can significantly jeopardize the structural stability and mechanical properties of welded joints. Porosity produces spaces within the weld metal, deteriorating its total toughness and load-bearing ability. These gaps act as tension concentration factors, making the weld much more at risk to splitting and failing under applied lots. In addition, porosity can reduce the weld's resistance to corrosion and other ecological factors, further decreasing its durability and performance.
Welds with high porosity degrees have a tendency to exhibit reduced impact stamina and reduced capacity to deform plastically prior to fracturing. Porosity can impede the weld's ability to efficiently transfer pressures, leading to early weld failure and potential safety risks in vital frameworks.
Finest Practices for Porosity Avoidance
To improve the structural integrity and quality of welded joints, what specific measures can be implemented to minimize the event of porosity throughout the welding procedure? more info here Utilizing the appropriate welding technique for the specific product being bonded, such as changing the welding angle and gun position, can additionally protect against porosity. Normal evaluation of welds and prompt remediation of any type of issues recognized during the welding procedure are vital practices to protect against porosity and create high-quality welds.Importance of Appropriate Welding Strategies
Applying proper welding methods is paramount in guaranteeing the architectural honesty and high quality of bonded joints, constructing upon the foundation of reliable porosity avoidance actions. Welding techniques straight impact the total strength and sturdiness of the welded framework. One key facet of appropriate welding techniques is preserving the appropriate warm input. Too much warmth can result in increased porosity because of the entrapment of gases in the weld pool. Alternatively, insufficient warmth may cause incomplete combination, creating prospective powerlessness in the joint. Additionally, using the suitable welding specifications, such as voltage, current, and take a trip rate, is crucial for accomplishing audio welds with minimal visit this site porosity.In addition, the choice of welding procedure, whether it be MIG, TIG, or stick welding, need to align with the specific demands of the project to ensure optimal outcomes. Proper cleansing and preparation of the base steel, along with picking the ideal filler product, are also vital parts of competent welding methods. By sticking to these best practices, welders can reduce the risk of porosity formation and produce top notch, structurally audio welds.
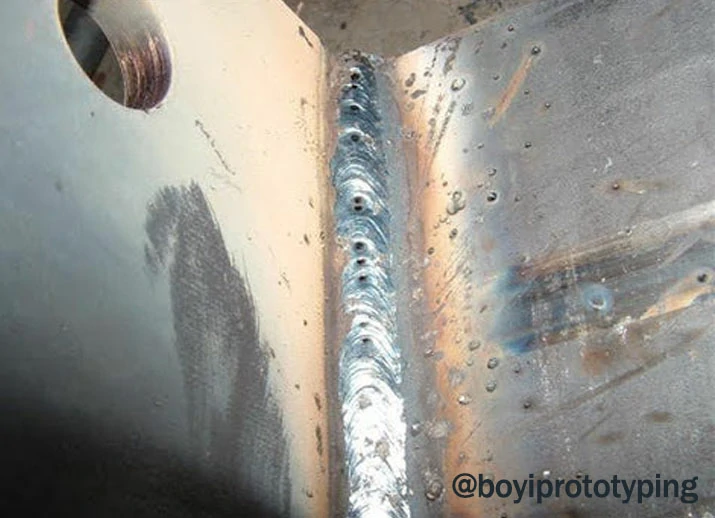
Checking and Top Quality Control Steps
Quality control procedures play a critical duty in verifying the integrity and reliability of welded joints. Evaluating treatments are necessary to discover and protect against click to find out more porosity in welding, making certain the strength and durability of the last item. Non-destructive screening techniques such as ultrasonic testing, radiographic screening, and aesthetic assessment are generally utilized to determine possible defects like porosity. These techniques permit the analysis of weld top quality without endangering the stability of the joint. What is Porosity.Performing pre-weld and post-weld evaluations is additionally important in maintaining quality assurance requirements. Pre-weld inspections include verifying the products, equipment setups, and cleanliness of the workplace to avoid contamination. Post-weld inspections, on the various other hand, assess the final weld for any kind of problems, consisting of porosity, and confirm that it satisfies specified requirements. Carrying out a detailed quality control strategy that includes complete testing procedures and examinations is critical to minimizing porosity issues and guaranteeing the total quality of welded joints.
Verdict
To conclude, porosity in welding can be a typical concern that influences the top quality of welds. By identifying the common root causes of porosity and executing best methods for prevention, such as appropriate welding methods and testing actions, welders can guarantee excellent quality and reputable welds. It is important to focus on avoidance techniques to lessen the incident of porosity and preserve the stability of welded structures.Report this wiki page